How Manufacturing Trends 2025 Are Impacting Manufacturing Recruitment
- Abhishek Bhosale
- Mar 28
- 5 min read
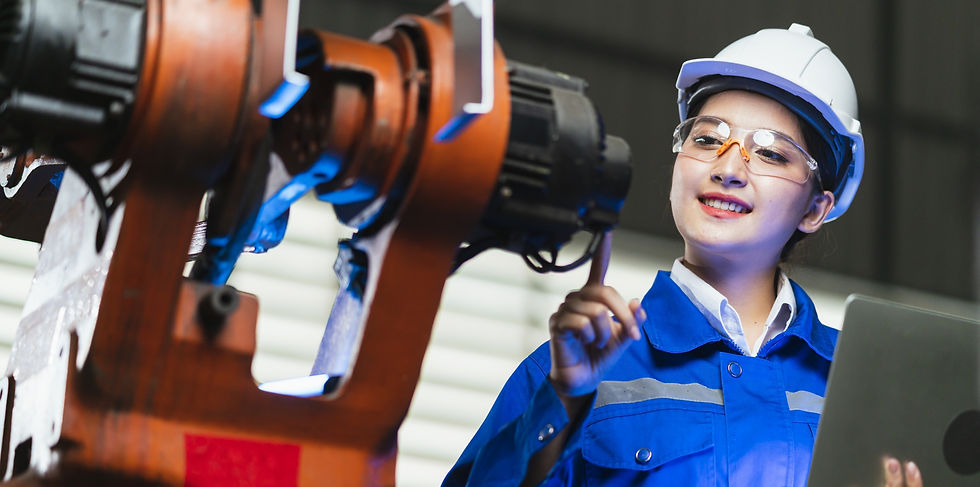
Manufacturing industry - what still comes to mind are the huge conveyor belts, manufacturing pipelines, shop floors, and workers intervening in each activity.
The manufacturing sector is at an inflection point in its history. This competitive advantage is defined by digital transformation at breakneck speed.
After weathering years of economic turbulence, the US manufacturing sector stands at the edge of a long-awaited resurgence. 2025 projections paint a picture of renewed strength—revenues surging by 4.2%, capital investments climbing 5.2%, and a long-overdue spark of job growth. The tide is turning, and with it comes a wave of optimism, resilience, and the promise of a thriving future.
Technologies such as Advanced analytics, cloud computing, and artificial intelligence are more than just catchphrases; they are engines of exponential increases in productivity, turning semi-manual manufacturing factories into smart factories.
This change also brings a significant shift in hiring talent. The manufacturing industry is one of the oldest industries, its practices fall behind.
The U.S. will face a shortfall of 1.9 million manufacturing workers by 2033; 3.8 million positions will open up, but nearly half could go unfilled.
The industry needs to catch up with the latest talent needs as employers' and candidates' expectations, roles, and skill sets are evolving quickly.
This blog dives into the major trends influencing OEM hiring and how they are impacting the recruitment practices in the sector.
1. The Industry 5.0 Transition: More Technology, More Human

For years, the manufacturing industry has discussed Industry 4.0, which includes automation, robotics, and the Internet of Things. However, Industry 5.0, where people and technology coexist, is coming into being in 2025.
What is Industry 5.0?
Industry 5.0 is about the co-existence of humans and machines. No one replaces either of them. Following are the main features of the new industry revolution with AI & ML, Automation in the picture.
Collaborative robots, or cobots, are becoming commonplace. They help employees rather than replace them.
Demand for personalization in manufacturing necessitates both automation and human creativity.
Soft skills are more important than ever. Creativity, problem-solving skills, and flexibility are becoming just as important as technical knowledge.
Recruitment Impact: Manufacturing recruiters must source candidates who can navigate both digital and manual workflows. The ability to blend technical know-how with human decision-making is now a hiring priority.
2. AI and Digital Twins Are Reshaping Talent Needs
Predictive maintenance, real-time simulations, and AI-driven decision-making are making the headway in all industries. In manufacturing, they are changing the type of talent the industry needs. Digital twins (virtual replicas of physical systems) are transforming manufacturing processes. These transformations demand for following skills.
Engineers and operators must understand AI-driven diagnostics.
Digital literacy and skills are essential—even on the factory floor.
Data Analytics and Business Intelligence are becoming core competencies.
Recruitment Impact: Manufacturing recruitment agencies are seeing a surge in demand for AI-savvy candidates—from machine operators who can work with predictive maintenance systems to engineers who can interpret digital twin insights. Traditional roles are evolving, and hiring strategies must follow.
3. Supply Chain Disruptions Are Changing Hiring Strategies
Supply chains have always faced disruptions—natural disasters, trade disputes, shifting consumer demands, and supplier issues. Businesses have navigated delays, shortages, and cost fluctuations for decades. But, the scale and frequency of disruptions have grown, making resilience and adaptability more critical than ever in an increasingly complex global market. 2025 is making flexibility a core business strategy.
Nearshoring and reshoring are ramping up. More companies are moving production closer to home, creating regional job booms.
Multi-source supply chains mean manufacturers need supply chain experts who can navigate complex procurement networks.
Sustainability is a hiring factor. Companies are prioritizing green manufacturing, and that means hiring sustainability specialists.
Recruitment Impact: OEM recruitment is seeing higher demand for supply chain professionals, procurement specialists, and logistics experts. Manufacturers need talent who understand local regulations, supply chain tech, and sustainability mandates.
4. The Workforce Shortage: Bridging the Skills Gap
The manufacturing labor shortage isn’t just a challenge—it’s a turning point. Companies that see this as an opportunity to rethink hiring, training, and retention will gain a competitive edge. Those who adapt to innovative workforce strategies will secure skilled talent and stay ahead in an evolving industry.
Upskilling & reskilling are essential. Employers are investing in training programs instead of just competing for the same talent.
Diversity & inclusion matter. Manufacturers are widening their talent pools, tapping into underrepresented groups.
Younger workers demand flexibility. The old 9-to-5 shift model is being replaced by hybrid work where possible.
Recruitment Impact: Manufacturing recruitment agencies are shifting from traditional hiring models to skills-first recruitment. Instead of only seeking industry veterans, companies are now open to hiring from adjacent industries and upskilling new talent.
5. The Rise of Mid-Tier AI and Automation Jobs
Not every manufacturing company needs or is chasing full automation for their processes. Many are focusing on mid-tier AI applications—tools that boost efficiency without eliminating human roles.
Predictive maintenance technicians who can help assess the upcoming risks, failures, or halts.
AI-assisted quality control analysts who are empowered to focus on the core part of improving the quality.
Automation integrators who bridge tech and traditional processes
Recruitment Impact: Manufacturing recruiters must identify talent that can work alongside AI—not compete with it. The best hires will be those who can integrate automation into existing workflows rather than replace human oversight entirely.
How Talent Sourcing can Impact Manufacturing Recruitment
Talent sourcing is a process of attracting, finding, and engaging talent to convert them into active applicants. This helps organizations build a sustainable talent pipeline to hire when the need arises.
For the manufacturing industry, as the needs are changing drastically which requires candidates to be digitally literate from level 0, mapping such talent beforehand becomes crucial.
A distinct function of talent sourcing for manufacturing talent can help access such niche, unique requirements. With the process such as Rent-A-Sourcer’s process of S-O-Q-S (Source, Outreach, Qualify, and Schedule) can empower recruiters to focus more on closing candidates than starting recruitment from scratch.
The Hiring Landscape in 2025: What’s Next?
Manufacturing is evolving at breakneck speed—but hiring strategies must move even faster. The ideal candidate isn’t just technically skilled; they bring adaptability, problem-solving, and digital fluency to the table. AI, automation, and smart systems are reshaping production lines, making digital skills as critical as hands-on expertise.
Reshoring is fueling regional hiring surges, but talent shortages loom large. The solution? Flexibility and upskilling. Companies that invest in workforce development will outpace those still chasing yesterday’s skill sets.
Manufacturing recruitment in 2025 isn’t just about filling vacancies. It’s about building a resilient, future-ready workforce that can navigate change and drive innovation. The manufacturers that get hiring right won’t just keep up—they’ll lead.